五金沖壓件AI視覺檢測(cè)應(yīng)用案例
在五金沖壓件的生產(chǎn)過(guò)程中,微小缺陷(如裂紋、劃痕、變形、毛刺)和尺寸精度問(wèn)題直接影響產(chǎn)品良率。某汽車零部件制造商引入AI視覺檢測(cè)系統(tǒng),解決了傳統(tǒng)人工檢測(cè)效率低(漏檢率高達(dá)5%)、成本高且無(wú)法適應(yīng)高速流水線的問(wèn)題。
技術(shù)方案采用"高精度工業(yè)相機(jī)+深度學(xué)習(xí)算法"架構(gòu):
1. 硬件配置:搭載5000萬(wàn)像素線陣相機(jī)與多角度環(huán)形光源,實(shí)現(xiàn)0.02mm精度的表面成像,覆蓋沖壓件360°檢測(cè)區(qū)域;
2. 算法模型:基于改進(jìn)的YOLOv5架構(gòu),通過(guò)遷移學(xué)習(xí)訓(xùn)練出缺陷識(shí)別模型,支持20+類缺陷分類,結(jié)合ResNet網(wǎng)絡(luò)進(jìn)行尺寸公差分析;
3. 邊緣計(jì)算:部署工業(yè)級(jí)GPU邊緣計(jì)算設(shè)備,單件檢測(cè)時(shí)間壓縮至0.8秒,滿足每分鐘60件的高速產(chǎn)線需求;
4. 數(shù)據(jù)優(yōu)化:采用生成對(duì)抗網(wǎng)絡(luò)(GAN)擴(kuò)充缺陷樣本庫(kù),解決初期數(shù)據(jù)不足問(wèn)題,模型準(zhǔn)確率從92%提升至99.5%。
實(shí)施:
- 檢測(cè)效率提升400%,實(shí)現(xiàn)全自動(dòng)在線檢測(cè)
- 漏檢率降至0.3%,年減少質(zhì)量索賠超200萬(wàn)元
- 替代3班倒的15檢團(tuán)隊(duì),節(jié)省人力成本30%
- 系統(tǒng)支持7x24小時(shí)穩(wěn)定運(yùn)行,兼容50余種沖壓件型號(hào)
該案例驗(yàn)證了AI視覺在復(fù)雜金屬件檢測(cè)中的突破性價(jià)值:通過(guò)多模態(tài)數(shù)據(jù)融合與自適應(yīng)學(xué)習(xí)機(jī)制,系統(tǒng)可識(shí)別傳統(tǒng)算法難以的隱性缺陷(如0.1mm級(jí)微裂紋),并自動(dòng)生成SPC統(tǒng)計(jì)報(bào)表指導(dǎo)工藝優(yōu)化。目前該方案已擴(kuò)展應(yīng)用于精密彈簧、金屬鑄件等場(chǎng)景,推動(dòng)制造企業(yè)向智能化質(zhì)檢轉(zhuǎn)型,為工業(yè)4.0升級(jí)提供關(guān)鍵技術(shù)支撐。
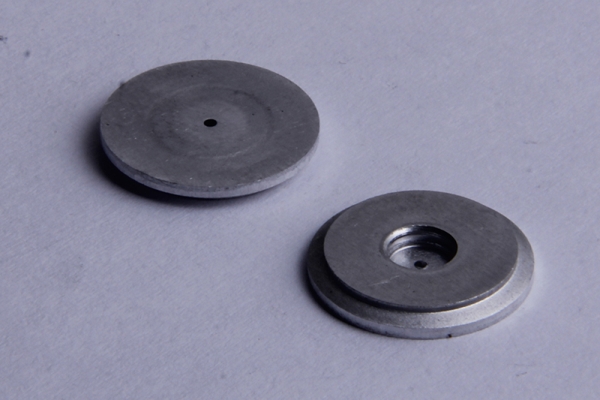
下一條:沒(méi)有了